John Oxley Restoration
Update August 2007
John Oxley 80th Birthday
On 21st July 2007 we celebrated the 80th anniversary of her launching date with a party at the Rozelle Heritage Shipyard. Read more about the shipbuilders and the party.
Hull
Hull Lines Drawing
We have never had the original lines plan, but there is a hull shape drawing included on the original 1927 Docking Plan. This drawing was used to inform dockyard staff about the shape of the underwater hull and the position of bilge keels and any relevant sea valve openings.
An accurate lines plan is required both to satisfy the Maritime Authority and to allow our honorary naval architect to produce a computer generated stability and flotation model. Essentially, this information is needed so that we can determine where the water line will be, and to calculate how stable the completed ship will be.
Volunteer worker and shipwright surveyor Tony Blakelock undertook the task of measuring the shape and verifying the existing1927 hull shape drawings.
A quiet day without much site activity was chosen. First step was to drop plumb bobs down from the stem and the stern. These were used to accurately mark the position of the John Oxley hull onto the steel deck of the Sea Heritage Dock.
From these datum points, the length of the hull was accurately measured and hull shape station points determined. These were marked permanently into the steel deck of the Sea Heritage Dock with centre punch marks.
Fortunately, our hull adequately matches the 1927 drawings and this information will be used to generate the final lines plan.
Hull Restoration
We have been struggling for some time to find a method for removing bitumen and fuel oil residues that contaminated the lower bunker space. The bitumen causes unacceptable fumes when in contact with oxy torches and had to be removed.
Conventional methods, such as steam cleaning or water blasting, result in a huge mess and possible loss of contaminants to the environment.
An innovative and high tech method was suggested, with a sponsor company offering their services to blast clean our surfaces using pellets of CO2 or dry ice. These pellets are blown at the oily residues with considerable force. On impact, they freeze the contaminant and then get behind it and blow it away. The cleanup task is minimal, and there is no liquid runoff to contaminate the environment.
Riveting
The forward keelson in the main forward hold has been re-fabricated and riveted. The riveting rate is well up on earlier figures – our minimum rate calculated to undock the vessel on time is 150 per week.
Like many activities, riveting is dependant on preparation. First, the old hull plates are removed, flattened when necessary, and then clamped to new steel plates where they function as drilling templates. Only when all rivet holes are drilled can the old plate template can be removed. The plate is then oxy cut to the same size as the template and the edges are ground smooth. Any plate curvature is added by press or by heat setting. The plate is then returned to the ship and bolted back into place with tack bolts in every second hole, sometime every hole so that the plate is pulled in as tight as possible.
The actual riveting task is labour intensive and requires a rivet cooker, holder upper (our friends in the US call this person the “bucker”) and the actual riveter. Often a rivet passer is used to assist in getting the hot rivet into its location as quickly as possible.
Riveting concentrated this year on the Port side in summer as the crew was chasing the shade. Riveting transferred to the sunnier and marginally warmer Starboard side in winter. Most of the hull is now chocked up on B-strake – there is the need for ship’s weight to be carried onto B-stake while A-strake is being removed.
The metal fabricators have also been working up methods for driving the 1 inch (25 mm) keel rivets. These are much larger than the ¾ inch (19 mm) hull rivets and must hold A strake hard against the keel. As the keel rivet holes are countersunk on both sides, the rivet heads need to be hammered from both sides. The image shows the team working up a technique to first rivet one side of the keel rivet heads, and then transfer to the other side, all before the hot rivet has cooled.
Engineering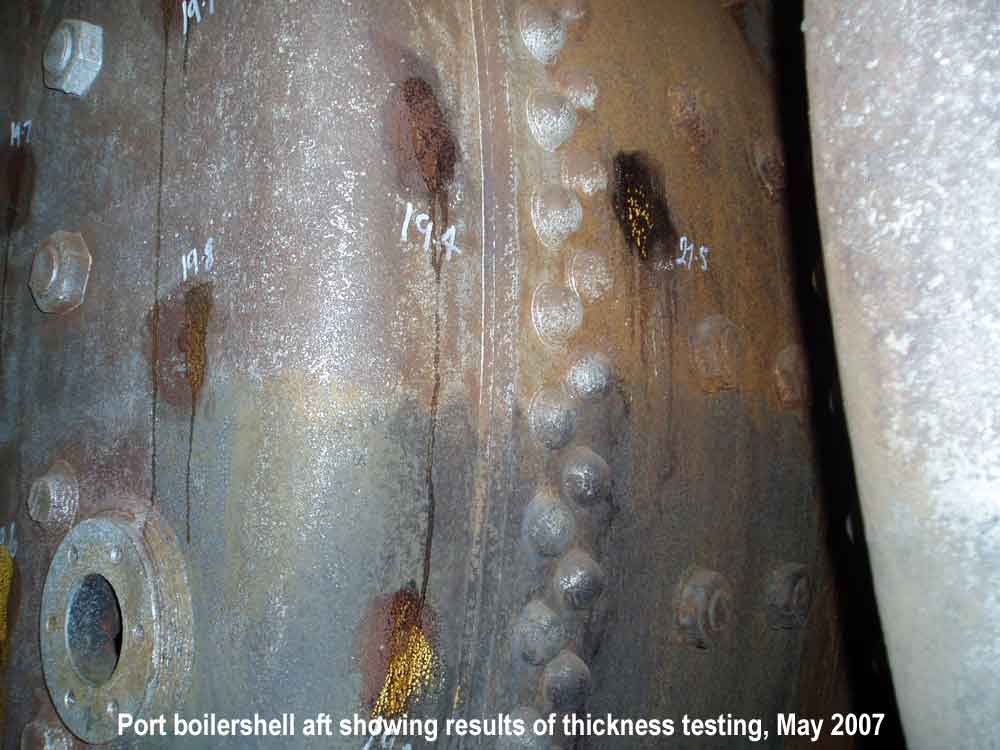
The NSW Heritage Commission has given a grant for the refurbishment of boilers. The thickness testing of the boiler shells is largely complete and results so far are promising. Some defects have been noted and repair procedures will be drawn up for each. Some 50 tubes are marked for removal and a method for removing these without use of oxy has been developed.
Suspected deterioration at the lowest rear flange of each boiler must be carefully inspected – sponsors HVT Inspections will undertake radiography of these parts to determine the extent of any defects discovered.
Fan and Fan Engine
The forced draft system on board John Oxley is of the Howden patent type, and consists of a Howden enclosed steam engine direct driving a centrifugal fan of about 54 inch (1.4 m) diameter. This fan supplies a large amount of low pressure combustion air to the furnaces.
The entire fan, engine and air ducting system have been removed to gain better access to the hull for repairs to frames and plating.
The fan itself, along with all the ducting, was suffering from the usual “rust bust” problem – this is when rust forms between the riveted joint surfaces and then wedges the joints open. If left unchecked, the joint will eventually fail.
The fan and ducting could not be reinstalled in this condition. Volunteer Don Harvey undertook the task of dismantling and chipping rust away inside every bulging joint in the fan. With a coat of quality rust primer the fan assembly was ready to be re-riveted back together.
Riveting small 3/8 inch (9 mm) rivets is more awkward than the larger rivets. Small rivets retain heat for only a short period of time – not really long enough to position, hold up and then rivet. It was noted that the fan was originally machine riveted and a way to duplicate this process was sought.
The solution was to construct a small-scale hydraulic riveter using some slab steel donated by the yard next door, plus a 10 ton Enerpac hydraulic cylinder. Rivet snaps were turned-up from old high-tensile bolts.
With the fan firmly tack-bolted together – each rivet was put in place and our hydraulic riveter positioned – an oxy torch was then used to heat the rivet and the hydraulic riveter used to quickly close each riveted joint. The other advantage is that there is not the usual noise racket associated with riveting.
The Howden enclosed steam engine is of a very robust design. The engine needed the usual repairs, including a reground crank, newly poured white metal bearings, reground piston and valve rods, new piston rings and lots of TLC
When dismantled, the crankshaft was hardchromed and ground to original dimensions. The main bearings were re-metalled with new white metal and were line bored at Halliday Engineering. Long time volunteer Wes Mallit then bedded in the crankshaft in the time honoured process – using bearing blue to mark the high spots on each white metal bearing half, which are then scraped away until each bearing closely matches the crankshaft.
More on this project in the next update.
Volunteering and Support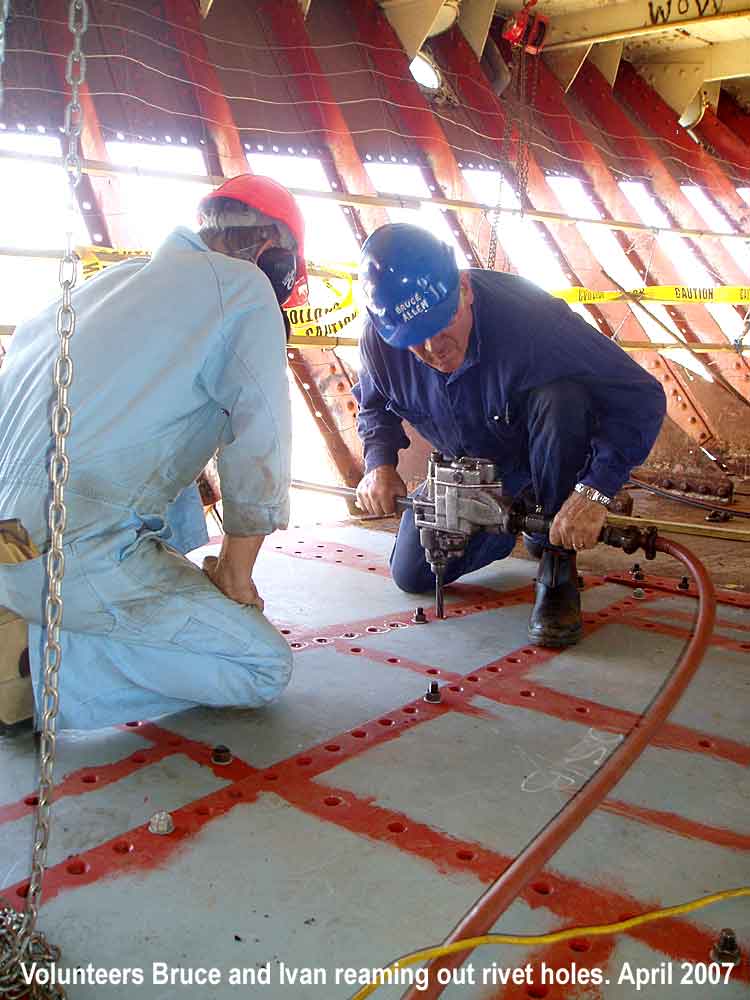
The core of skills needed to restore and then operate heritage ships is diminishing in the broader community.
A vital part of Sydney Heritage Fleet work is the preservation of traditional skills through restoration work on actual heritage vessels and much of this work is learnt and practiced by keen and enthusiastic volunteers.
Heritage Fleet volunteers come from all walks of life and consists of both the young and not so young. We have men, and an increasing number of women, on site – all are united by the drive to progress work on John Oxley.
Some of our workforce bring valued ship repair or similar skills to the project – many others turn up and quickly learn useful skills on site that makes them very productive volunteers.
Those who wish to join up can contact our office on 9298 3888 and ask to attend our next tour group.
Main work days are Tuesdays, Thursdays or Saturdays – visit on one of these days and ask to speak with one of the team leaders.
Supporting the Project
The success of our restoration is primarily about what sponsors, supporters and volunteers bring to the project. Without the generosity of so many people, the project would not be moving ahead so successfully.
Many companies and businesses assist by donating or discounting their services, or by supplying materials and funding.
This restoration with its non-profit status and hard working workforce certainly inspires others to get involved with the project – if businesses or individuals feel they are in a position to help, please make contact through 9298 3888.